-
Senior Member
-
Senior Member
Once Dave decided he wanted a roller cam, I suggested changing the original dual plane intake to a single plane, figuring it would work better with higher rpm. I tried a Dart single plane intake, but it would not clear the ridge on the 990 heads, so I spent a few minutes thinking about grinding the edge of the intake,, or removing the heads and grinding them,,, wasn't excited about either. I had offered to get the Dart intake polished, but Dave declined, so while I was looking over the problem, I decided to get a polished Professional Products intake that would compliment the look of the new Quick Fuel carb, Rex stainless steel scoop, and fabricated Obnoxious Racing Engines valve covers that still had not arrived.
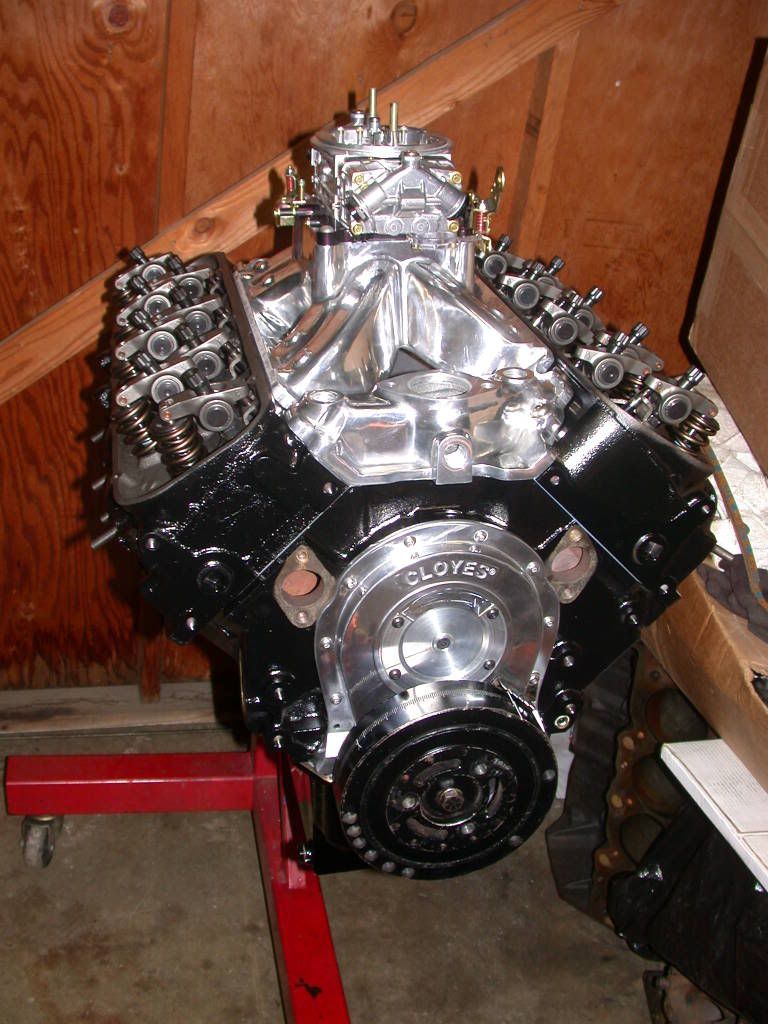
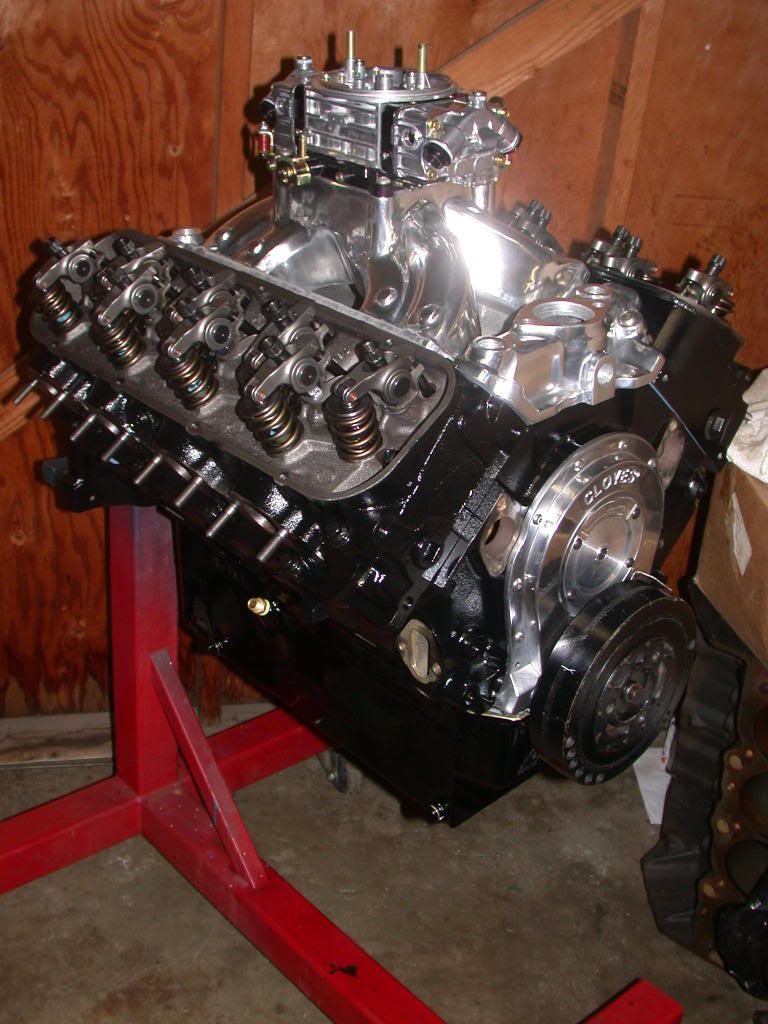
-
Senior Member
-
Senior Member
-
Senior Member
I somehow opted to set the timing at 34 degrees total for the first pull, even though I would normally think about 36 degrees. Coupled with the custom Quick Fuel 850 CFM carb that was built to match this engine's specs, right down to cam size, jet boat application, RPM range, and even my guess at horsepower, the first pull on the dyno was almost equal to the best we made for the day. A second pull so that Mike could have a better feel for the torque of the engine netted a best of 606 horsepower at 6300 rpm, and 566.9 ft/lbs torque at 4800-5000 rpm, with torque numbers over 500 ft/lbs between 4000 and 6000 rpm.
We did pulls with 36 degrees of timing,, and also jetted down a couple of sizes looking for more heat and power, but both dropped a little bit of power.
I chose to run Torco Racing Oil for the dyno runs since it was available right there, even though I normally would just recommend running something that is easy to get anywhere, such as Vavoline Racing Oil,, which many regular parts stores still sell. The dyno oil will be drained and the oil filter changed before it leaves to go into the boat.
The ratio of horsepower to cubic inches worked out at almost 1.3-1. I think we could have pulled more power with a touch more compression (remember this engine is only 9.6-1), but for what it is, it makes a lot of bang for the buck! I am pretty sure some guys with tunnel ram engines are going to be left scratching their heads when this clean little sleeper runs past them.
-
Senior Member
Tags for this Thread
Posting Permissions
- You may not post new threads
- You may not post replies
- You may not post attachments
- You may not edit your posts
-
Forum Rules
All times are GMT -7. The time now is 10:46 PM.
vBulletin Skin By: PurevB.com
|
Bookmarks