-
Senior Member
Mild pump gas 454 build and dyno test.
There was quite a bit of indecision by the owner on this build, to say the least. I tried to educate him as best I could as to the differences in size, power and cost, and after discussing 468 flat tappet, vs 496 and then roller cam options, he decided he wanted to go with the flat tappet 468. I had a nice rotating assembly with 7416 forged GM crank, GM rods and Arias forged pistons, along with some nice 990 heads. This engine is to go in an 18' jetboat, and the customer lives in Utah and runs at altitude. As it came closer to time to assemble his engine, there was talk about moving to the river, and I had 2nd thoughts about the compression ratio the domed Arias pistons would provide with the 990 iron heads, so made the decision to purchase new KB Icon forged pistons that would yield 9.6-1 compression that I deemed safe and appropriate for a pump gas iron headed engine. It was sometime later, after that assembly had come back from balance that he decided that it would be more fun to have a solid roller cam, and to dyno the engine, which meant he would like some bragging rights....hmm so now we have a mild compression engine that we were going to run a dual plane aluminum intake and single carb, hmm might have to give that some thought.
-
Senior Member
-
Senior Member
-
Senior Member
-
Senior Member
I am not able to shoot photos during the block washing process with the degreaser and water flying all over, but I normally do a complete 3 step wash, solvent or degreaser with brushes and scrubbing,, high pressure water through all passages, then a soap and water wash, applied with a high pressure sprayer,, more brushes and scrubbing, another high pressure application of a more diluted soap and water mix,, and then finally all oil passages rinsed with a very high pressure nozzle on the hose, every direction it can be accessed from.
The cylinders get oiled down as soon as they are blown out, and the block is allowed to dry prior to masking for paint. I have dedicated oil pan, timing cover and pipe plugs so that I can do a neat job and not get overspray on gasket areas. I use masking tape and paper to cover the top, tracing the outline of the head gasket rather than just a straight line of tape.
I also prefer to install the new brass freeze plugs prior to painting, since they won't stay shiny very long. I have always had excellent luck with Aviation grade Permatex(by Loctite now) brushed into the holes in the block carefully, so there won't be a bunch on the surface I want to paint.
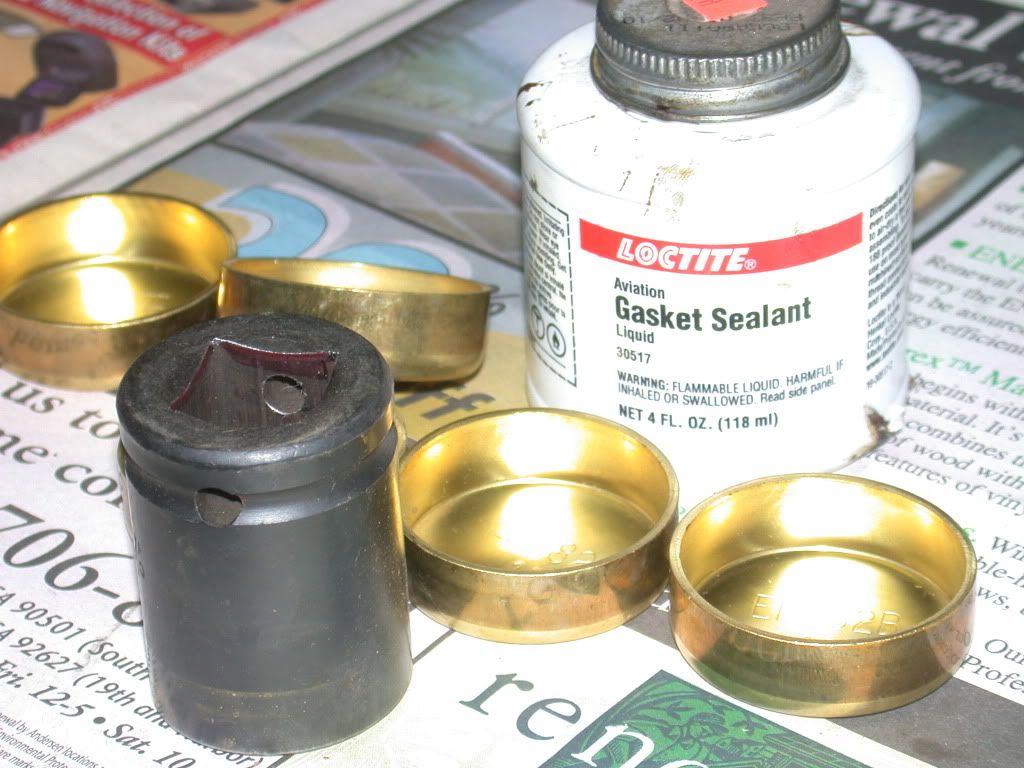
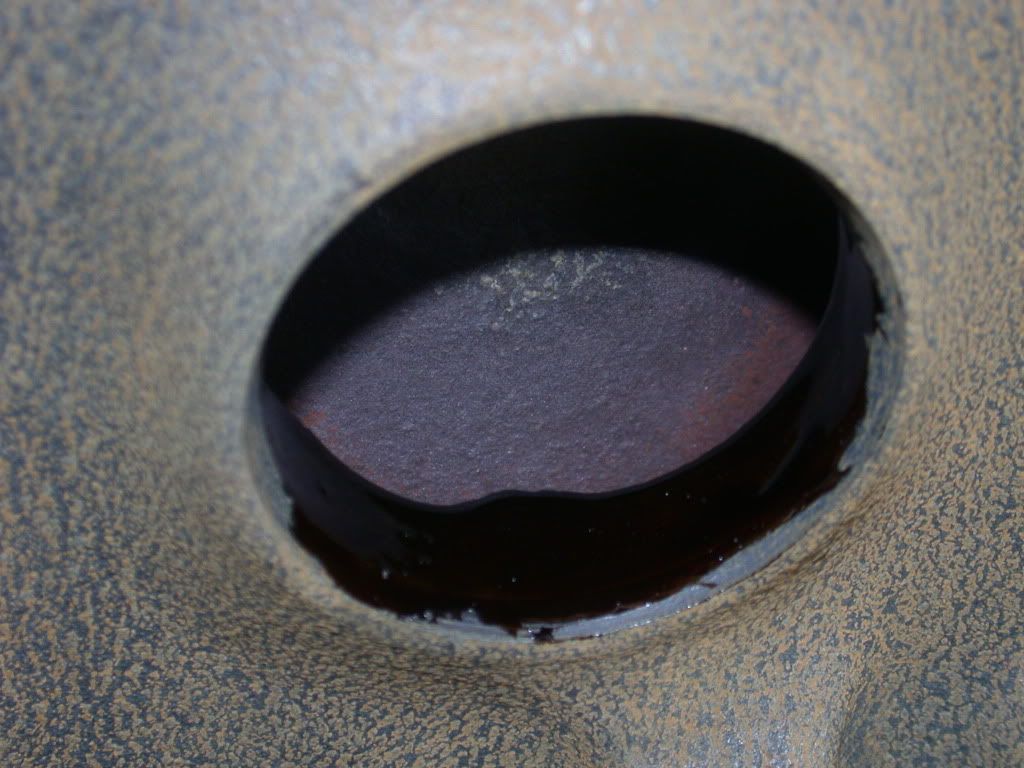
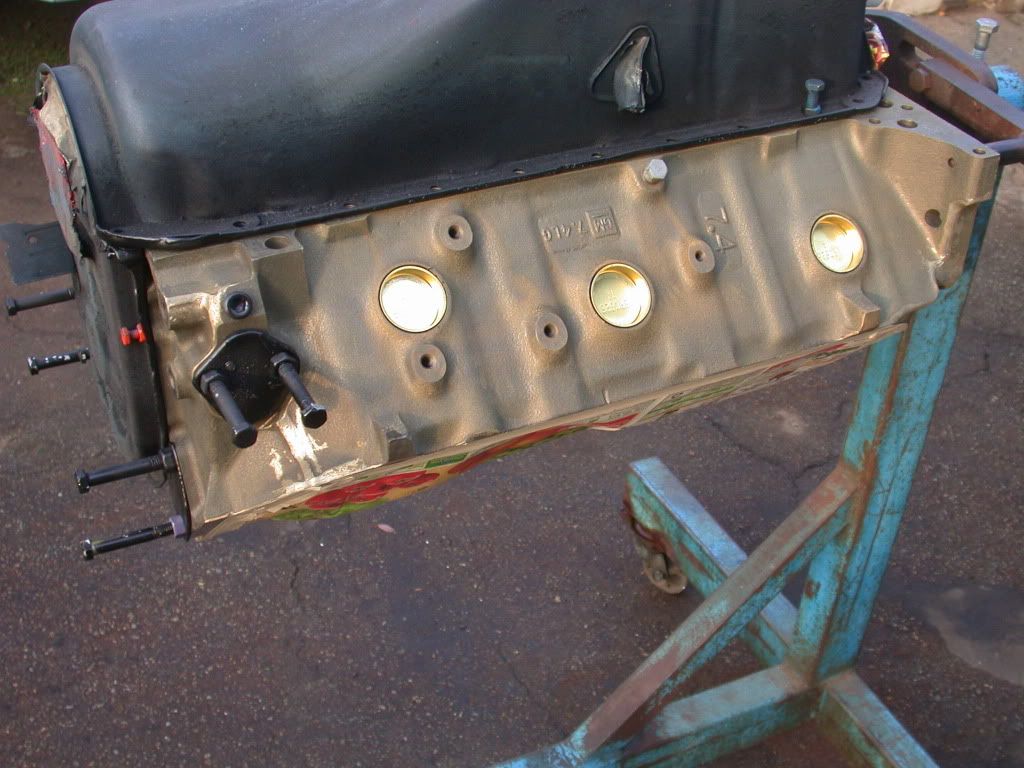
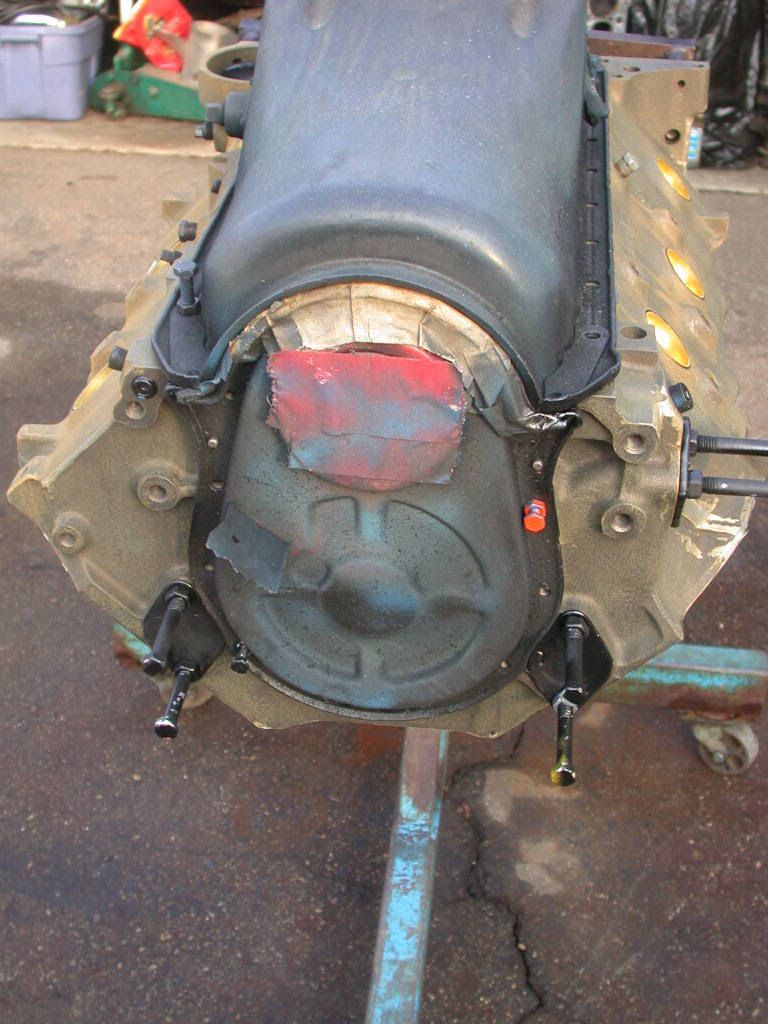
-
Senior Member
-
Senior Member
Then valley screens are epoxied into the valley since it's a roller cam engine, just in case there is a problem with a lifter tie bar or something, to help prevent debris getting into the bottom end and beating parts up.
-
Senior Member
The crankshaft was measured, and bearing clearances determined by torquing bearings in place. I guess I didn't get photos of the mains being measured on this one, but here is one of the rods being checked with the dial bore gauge.
-
Senior Member
-
Senior Member
Tags for this Thread
Posting Permissions
- You may not post new threads
- You may not post replies
- You may not post attachments
- You may not edit your posts
-
Forum Rules
All times are GMT -7. The time now is 04:20 PM.
vBulletin Skin By: PurevB.com
|
Bookmarks